お疲れさまです
くおりです~
今回はクレーム対応事例で【微生物汚染】を紹介します
「印字不良・印字なし」「異物混入」は別で解説させてもらっています
微生物汚染については腐敗しやすい製品や、工程での加熱不足がクレームの原因となります
これも来るとかなりやばいです
多くの場合はロット回収の対象となるでしょう
重篤なクレームです
もし発生したしまった時に拡大の範囲を特定すること
そして対象の範囲への対応を決めるのが大事となります
企業責任としても事前に準備しておきましょう
前提ですがクレーム対応は毎回同じようには対応出来ません!!
最終的には個々の対応になりますが確認事項は共通事項があります
皆さんの参考になればと思います
今回のこの段落で説明していきます
- 全体の対応の流れ
- 原因追求のコツ
- 修正と是正
- お客様対応
では早速説明していきます
全体の対応の流れ
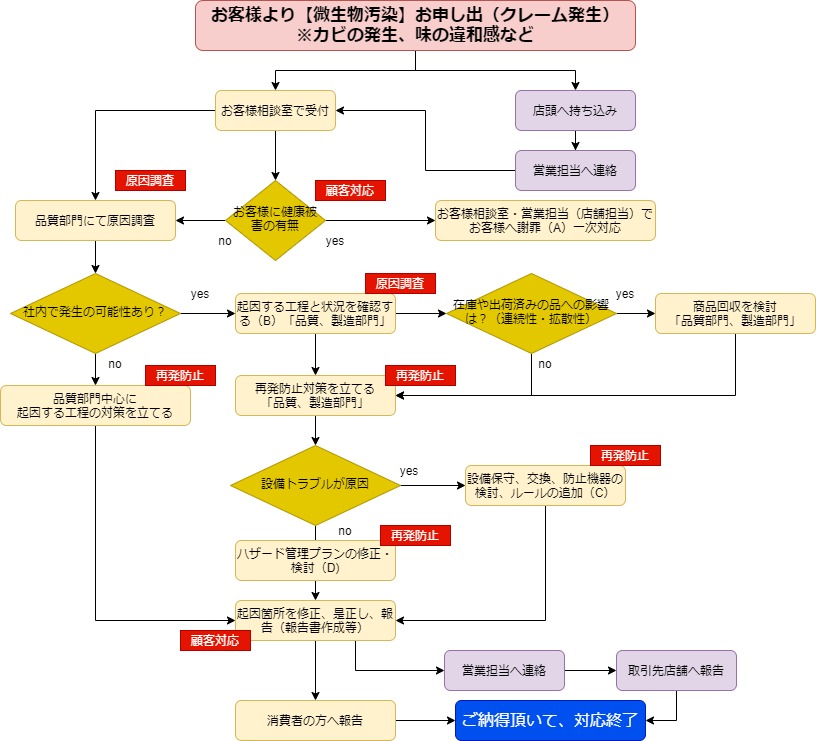
全体の流れについては上記の図で示しました
それぞれの会社でも「クレーム対応マニュアル」「商品回収マニュアル」があるのではないでしょうか
一度照らし合わせて、不足があれば追加してみてください
個別に説明していきます
微生物汚染が発生したら、社内のお客様相談室や店頭へのお申し出から対応が始まります
(A)一次対応
顧客の対応はお客様相談室、店舗への対応は営業担当がメインで行うこととなります
お菓子や砂糖などの原料関係では微生物汚染はほとんど考えられないかもしれません
それぞれの水分活性を確認した上で事実の確認をしましょう
微生物汚染でカビが発生したときにはお客様の健康被害はあまりないかもしれません
しかし、衝撃は大きいため、非常に精神的なショックが大きいです
病原微生物が生き残っており、食中毒になってしまった場合は傷害となります
それぞれPL保険も確認しながら健康被害も考慮し、一次対応を確実に行う必要があります
腐りやすい、腐敗しやすい生ものや惣菜などは食中毒の危険性があります
一次対応でお客様の最初のお申し出を聞かなくてはその後の対応で取り返すのは大変です
あくまで一次対応では調査前でこれから調査することと、お客様のことを気にかけて謝罪に徹しましょう
お客様の精神的ショックが大きいのは微生物汚染となり、しかも、子どもが食べてしまったときは大きな問題になることが予想されます
(B)原因が社外にある場合とは?
微生物汚染のほとんどは工程内での加熱不足や、品質保持剤が機能していないなどが原因です
ただ社外での可能性も否定はできません
考えられる社外での可能性は以下の通りです
- 消費期限を超えて保存されていた
- 冷蔵や冷凍保存のものが常温で置かれていた
- 配送途中や店頭で製品の包装が破れて、密閉性が失われた
クレームの原因がどうしても不明で、なおかつ、お申し出が1件しかない場合では、社外での可能性が考えられます
「クレームの原因がどうしても不明」という管理を出来ていることが前提となりますので、普段の生産ルールの遵守や記録の管理を確実に行うことが必要です
現場の作業者にも「いざという時に自分たちの原因ではないようにしっかり記録しよう」という声かけはおすすめです
(C)設備対応を中心に対策をする
設備に原因が起因する場合は設備の修繕、保守が必要です
しかしながら人に起因する場合でも設備の対策が必要かもしれません
ラインでの生産に置いては人がトラブル時に対応して、その対応後に加熱不足のものが流出することがあります
これは、人の行動で目の前のトラブルへの対応に集中し、その不具合のある製品自体への注意が弱まってしまうことにあります
そのため、人がトラブル対応時に誤って発生してしまったのであれば、人が後工程に簡単に流せないこと対策の一つとなります
具体的にはアラームが鳴る、ラインが停止する、エリアを分ける、制御をするなどがあります
(D)ハザード管理プランの変更・検討
加熱工程のほとんどはCCP担っているのではないでしょうか
特に殺菌を行うボイルやレトルトに置いては特別に設けられた工程であり、CCPとしてモニタリングやその逸脱時のルールが決められていたはずです
まず最初に、そのルール通り行っていたかを確認しましょう
もし、ルール通りに行っていたのにクレームが発生してしまった場合は、ハザード管理プランの変更が必要となります
クレームはPDCAの検証、Checkに当たります
クレームが発生したということは運用のDOが間違っていたということの証明です
特にCCPについてなので、CCP工程の見直しが必要です
加熱の温度を上げるのか、時間を長くするのか、逸脱時の対応のルールを変更・追加するのか食品安全にチームを中心に協議・検討し、より確実なルールを作りましょう
全体の流れ
原因を特定し、対策し、それをお客様やお店様へ報告し、ご納得いただいたら始めて対応完了です
原因を特定し対策をすることがクレーム、お申し出の対応ではありません
最終的にお客様がご納得いただくことが対応の完了です
また、製品に連続性や拡散性がある場合には次のクレームにつながらないようにしなくては行けないのでこちらもお忘れなく
過去の回収判断の記事を参考にしてください
原因追求のコツ
原因追求のコツをお伝えします
経験者にはアタリマエのことかもしれませんが、改めて抜けがないか確認しましょう
ステップ1.考えられる原因は製品で異なる
製品によって微生物汚染の原因は異なります
大きく分けると、加熱不足(温度と時間の未達)、包装不良、品質保持剤の機能不全、製品への菌の異常な付着があります
加熱不足(温度と時間の未達)
工程上で加熱工程があったが、そこでの殺菌不足が原因となります
- 加熱するセンサーが故障しており、数値が異常だった(制御出来ていなかった)
- 加熱器自体が故障し、規定時間で殺菌できなかった
- 加熱温度は人が管理していたが、未達の状態で仕上げた(急いでいたなど)
- タイマーが故障しており、規定の時間の加熱がされなかった(制御できていなかった)
- そもそもレトルトなどの殺菌工程を経ずに製品化してしまった(人が間違えて後工程へ流した、置き場の取り違えによるレトルト未殺菌など)
- 設定していた条件がギリギリで、季節変動や、原料の状態によっては菌が発生してしまう条件であった(そもそもの設計段階での問題)
包装不良(空気の流入)
包装工程が起因する場合
- 包装はされているがピンホールがあり、外気が通ってしまっていた(酸素が残り菌が発生、アルコールが充満せず菌が発生)
- 包装時にシワ(ダーツやタック)があり、空気が通ってしまっていた(酸素が残り菌が発生、アルコールが充満せず菌が発生)
- 包装した際のシールが弱く、シール部分が衝撃で簡単に空いてしまう状態であった
- 包装時に品質保持剤を入れる予定が入っていなかった
品質保持剤の機能不全(脱酸素剤、アルコール製剤など)
包装は問題ないし、工程も問題ないときは品質保持剤の扱い方も疑いましょう
- 品質保持剤の使用期限を逸脱して使用していた(開封は1時間などの使用期限がありますよ)
- 包装不良で品質保持剤の使い回しをしていたが機能が低下していた
- 脱酸素剤で空気を吸う予定が、吸っておらず酸素が残っていた(初期不良も可能性があります)
製品への菌の付着
- 原料がいつもよりも菌が多い状態で納品された
- 原料の洗浄工程があるが、薬剤濃度が薄く、設備が不調で洗浄しきれていなかった
- 原料や製品を途中で落下させてしまったが、ラインに戻して使用してしまった
これらのパターンが考えられます
もし、他にも事例があればぜひ、コメントで教えて下さい!
ステップ2.社外での発生の可能性
上述しましたが、現場内社外での起因は以下の通りです
- 消費期限を超えて保存されていた
- 冷蔵や冷凍保存のものが常温で置かれていた
- 配送途中や店頭で製品の包装が破れて、密閉性が失われた
これらの可能性も含めて対策は検討していってください
わからないものはわからないという返答をすることと、その上でも推測し、対策をすることが次のお申し出の再発防止になります
決めずに曖昧なままではお客様への説明も出来ないので、諦めて推測に徹するのが最終ステップとなります
ステップ3.工程ごとで菌検査をして原因箇所を絞り込む
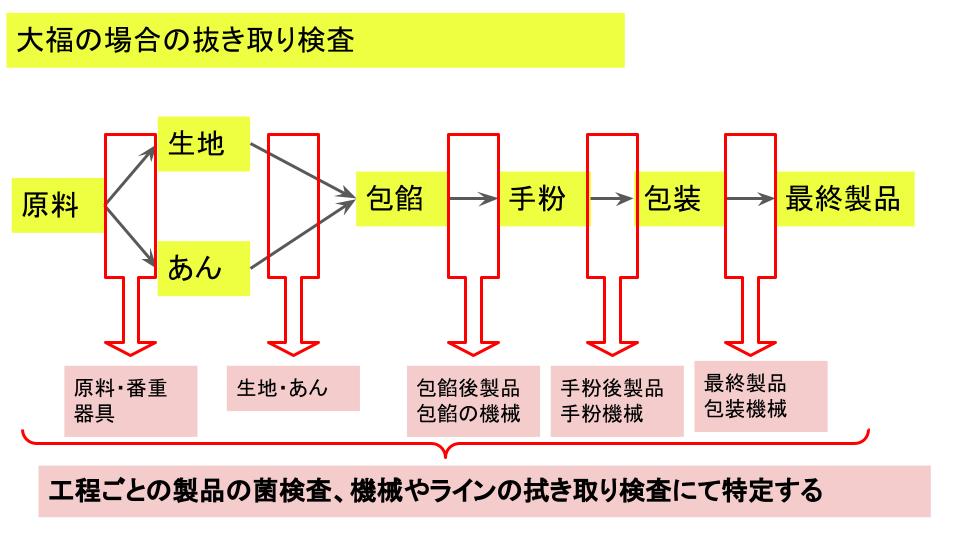
社内での可能性があり、最終製品では確かに菌が多いけど、どこかわからない場合
工程ごとで製品の菌検査、機械やラインの拭き取り検査にて汚染箇所の特定をします
最初から憶測がある場合はその前後の検査、検討がつかない場合は一通り工程ごとで製品検査をした上で、工程の拭き取り検査をすると汚染している工程がわかるでしょう
また、作業者を介して汚染されていることもあります
作業者の手洗い不足、作業着の洗浄不足、ほか作業場との交差汚染があります
人の手の拭き取り検査も場合によっては必要かもしれません
修正と是正
原因を特定したら修正と是正が必要です
修正は現状ある危害を取り除くこと、是正はその後に同じことが発生しないようにすることです
修正の際には、機器や原因を直したり、除去することと、製品に対する処置もしなくてはいけません
原因が連続性や拡散性が疑われる際に商品回収を実施するのも修正です
特に微生物汚染で工程に問題があり、連続性が否定できない場合は回収になります
そのため微生物汚染は重篤なクレームとなります
特にハザード分析のBCPのB:生物学的リスクと直結します
是正はその後の再発防止なので、人に由来するものであれば、作業者の力量を評価し、適切なスキルをもたせる、ルールの設置・遵守の方法・人の入れ替え時の教育、が対策となります
設備起因の場合は、設備の修繕、定期的な点検保守計画を設定するが対策となります
特に普段の生産内でのちょっとしたことに対策をしていれば防げたクレームは多くあります
作業者の関心や行動へ訴えかけることが最も効果の大きい対策となります
過去に記事を書いておりますので参考にしてみてください
微生物汚染での修正、是正でのポイント
微生物汚染が工程内で発生していた場合、多くは清掃・殺菌がメインとなります
清掃ルールを見直す際はその清掃前後や、やり方を変えたことで菌数や汚れ具合が減っているかを確認しながらやることで有効な清掃ルールを作れます
手洗いや作業者の衣服に関する汚染についてもルールの設定とともに、その遵守の状況まで見ることが大事です
交差汚染についてもルールの設定や、作業衣区域の分断、移動する際の右側通行のルールの遵守だけでも減少するかもしれません
微生物汚染は目に見えないため、普段の細かな作業者の行動でも効果が変わってきます
普段の5S活動を強化することが結果的に最も大きな効果が挙げられます
お客様対応のコツ
製造の部門にいるとどうしても抜けてしまいがちなのはお客様対応です
製造での原因や対策は最終的にお客様が納得するように実施しなくてはいけません
といっても無茶苦茶な要求は組織として費用がかかりすぎたり、人件費が高騰しすぎることにも繋がります
お客様対応でいちばん大事なのは、お客様にまずは謝罪し、意見を聞くことです
クレームや、お申し出を言ってきている時点で会社への「期待」があります
期待もなければ、クレームを言って「直してほしい」という要望はもちません
もちろん、クレーマーに近い人で金品やなにかもらえるかも!と期待する人もいます
ただ、手間をかけていることを考えれば、会社のことを一緒に考えてくれているファンとも言えます
お客様をファンとして捉えることができればお客様対応はうまくいきます
丁寧に、怒らせないようにと怯えて対応するよりも、ファンなので力になってくれている!と対応することが上手くいくコツになるでしょう
基本ですがS言葉を積極的に使い、D言葉を避けるように接するようにしましょう
S言葉(承認、受容の言葉)
すみません、承知しました、失礼しました、さようですね、そうですね
D言葉(逆説、反逆の言葉)
でも、だって、ですから、だから
S言葉、D言葉は普段のやり取りでも活用できます!
ぜひ試してみてください、しつこく意識することで習慣になります
自然とできるようになれば一流のお客様対応名人です
まとめ
今回はクレーム発生時で特に【微生物汚染】での事例を取り上げました
全体的な流れはどのクレームでも同様ですが、微生物汚染においてはお客様のショックと食中毒の可能性があることが問題です
そのため、連続性があれば即回収対象となります
しかも、回収の範囲は工程を管理していれば必ず特定でます
企業としての責任を全うするためにも微生物汚染には早急・確実な対応が必要となります
現場内の普段のトラブルやミスから発生の可能性を見つけ、事前に防ぐことが重要です!
事前の準備や心構えがクレームを速やかに完了させてくれますので改めて社内の対応について見ていってください
【異物混入】についても記事を書いており、それはこちらを参考にしてください
【印字不良・印字なし】についても記事を書いており、それはこちらを参考にしてください
ご意見お待ちしております
質問、ご意見お待ちしております
お問合せフォームからお送りください
ぜひ、一緒に考え、学び成長していきましょう
特にそれぞれの苦労話や、今悩んでいることがあれば、相談ください!
必ず返答させてもらいます
S言葉、D言葉を広めている援川さんの本です
コメント